Radiant Heat Cost + Overview Part 5/5 | MAD County Build
- MR Post Frame
- Mar 4, 2024
- 3 min read
Welcome back to MR Post Frame, everyone! Today marks part five of our in-floor heat series. I've linked the video that goes along with this post down below. In this installment, we'll delve into the cost breakdown of the system used in my build, focusing on today's prices. Prices have seen an increase since my initial setup, affecting certain materials. So, the costs you'll see are based on current market prices.

Before we dive in, I want to mention that if you're planning to design a barndominium, shop, garage, or any similar structure, feel free to check out our website for assistance. Additionally, for those looking to undertake a self-build, we have a Patreon group specifically for self-builders. It's a fantastic community where you can ask questions and share your build experiences. Check it out!
Now, let's jump into the cost breakdown of the in-floor heating system. If you've been following the first four parts, you already know the journey that brought us to this point. I'll break down the discussion into different phases.
Below Slab Heat:
The initial step involves preparing below the slab. Regardless of your building type, insulation and a vapor barrier are crucial underneath the slab, especially if you plan on having radiant heat. For this, you'd typically need radiant heat tubing, usually half-inch, 300ft loops of oxygen barrier PEX. In previous videos, we used pink board, but today we've switched to an EPS foam called Hitz Halter for various benefits. It includes a built-in vapor barrier on both sides, has termiticide for insect resistance, and provides convenient grid lines for laying out tubing and rebar.

If we compare costs, using pink board for my build would have totaled $12,613 in today's prices, while the Hitz Halter insulation brings it down to $10,597. This highlights a significant cost difference of $2,016.
Below Slab Process:
Preparing the site involves achieving a level building site with 4 to 6 inches of 3/4 to 1-inch rock beneath the slab for proper drainage. Frost protection is added once the structure is complete, typically with the help of a small excavator. The new installation method simplifies the process, making it DIY-friendly and efficient.
Boiler + Controls:

After the slab is in place, the next step involves installing circulators, zoning, manifolds, and the boiler. The cost for these components, including the boiler, controls, and related items, came to $9,450 in my case. The total cost for heating 4544 square feet was $2,632.47 using the old method and $441 per square foot using the new method.
Grand Total:
Considering all phases, the grand total for the old method is $485 per square foot, while the new method brings it down to $441 per square foot. Comparing costs for different-sized buildings, smaller structures tend to have higher costs per square foot due to fixed starting costs. However, the efficiency of the system makes it a worthwhile investment.
Questions Answered:
Addressing common questions, the preference is for gas boilers over electric boilers due to efficiency and suitability for larger spaces. The system is primarily water-based, and the decision to use glycol depends on factors like heating frequency and the risk of freezing.
Conclusion:

In conclusion, the cost of in-floor heating can be surprisingly affordable for its efficiency and comfort. Gas boilers are recommended, and while electric boilers may be suitable for certain scenarios, gas proves to be more efficient in larger spaces.
I hope this breakdown provides clarity on the costs associated with an in-floor heating system. If you have more questions or need assistance with your project, feel free to reach out.
Thank you,
MR Post Frame
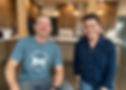
Patreon Group:
Interested in tackling your build on your own? If you want to explore the possibility of being your GC or self-building, our Patreon membership is for you! It's a community of like-minded people offering support, discounts, Q/A, and more.